Technologies
Sealing Solutions:
Sealing solutions are among the main industrial applications of rubber. Whether you’re looking for a
standard static seal such as O-Ring, Flat-Ring or Gasket or whether you’re looking for a
dynamic seal such as V-Ring, U-Ring, Rod Seal, Piston Seal, Wiper or Oil-Seal and especially if you are
in need for a complex and fully customized seal, molded or bonded, (links), our rubber and silicone
solutions are totally designed for your applications. By selecting the right high-performance
materials, the precise tolerances, the relevant molding technologies, and the correct test procedures
according to industry’s strictest quality standards, we assure long-lasting and uncompromised part’s
performance perfectly meeting your application’s requirements and specifications.
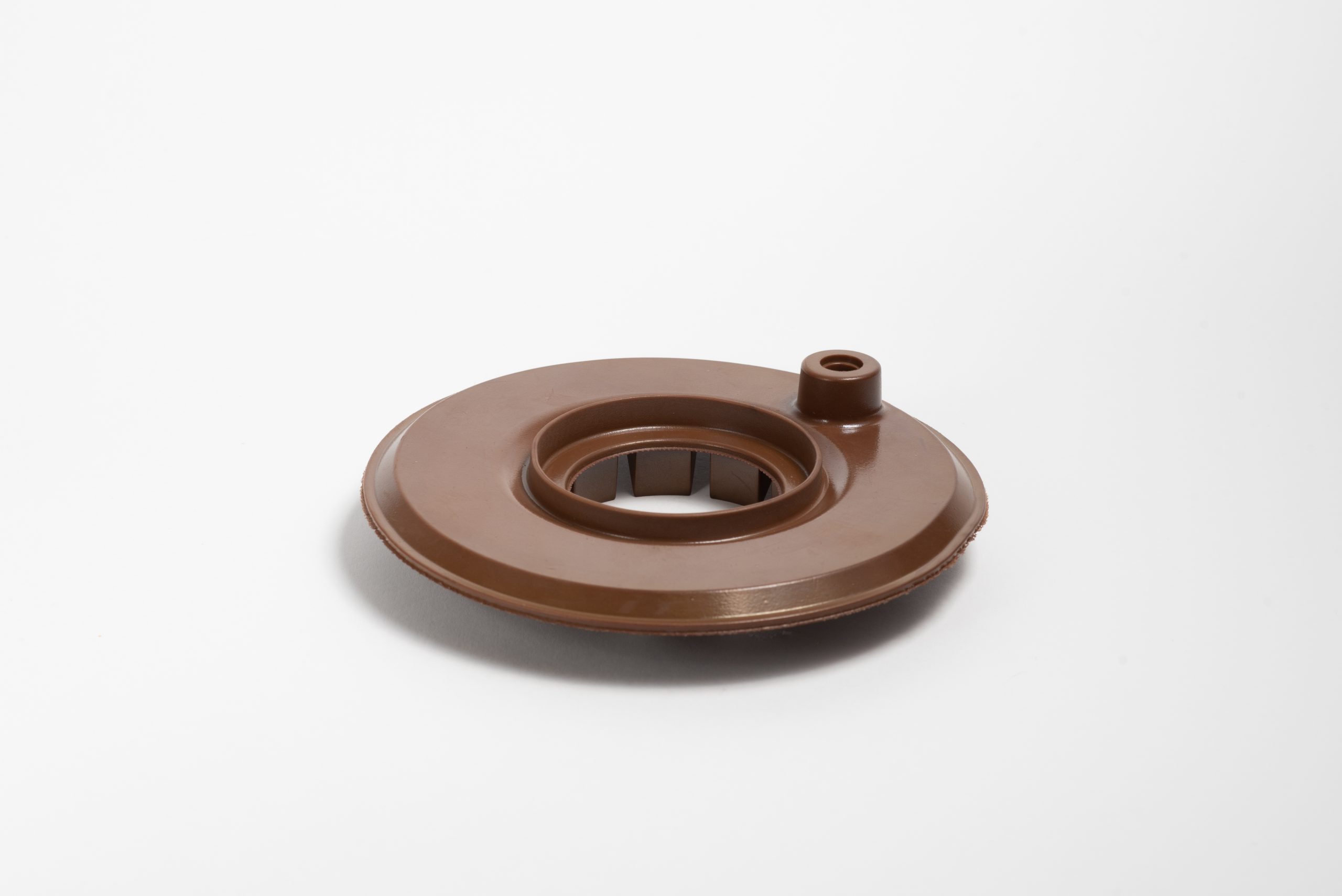
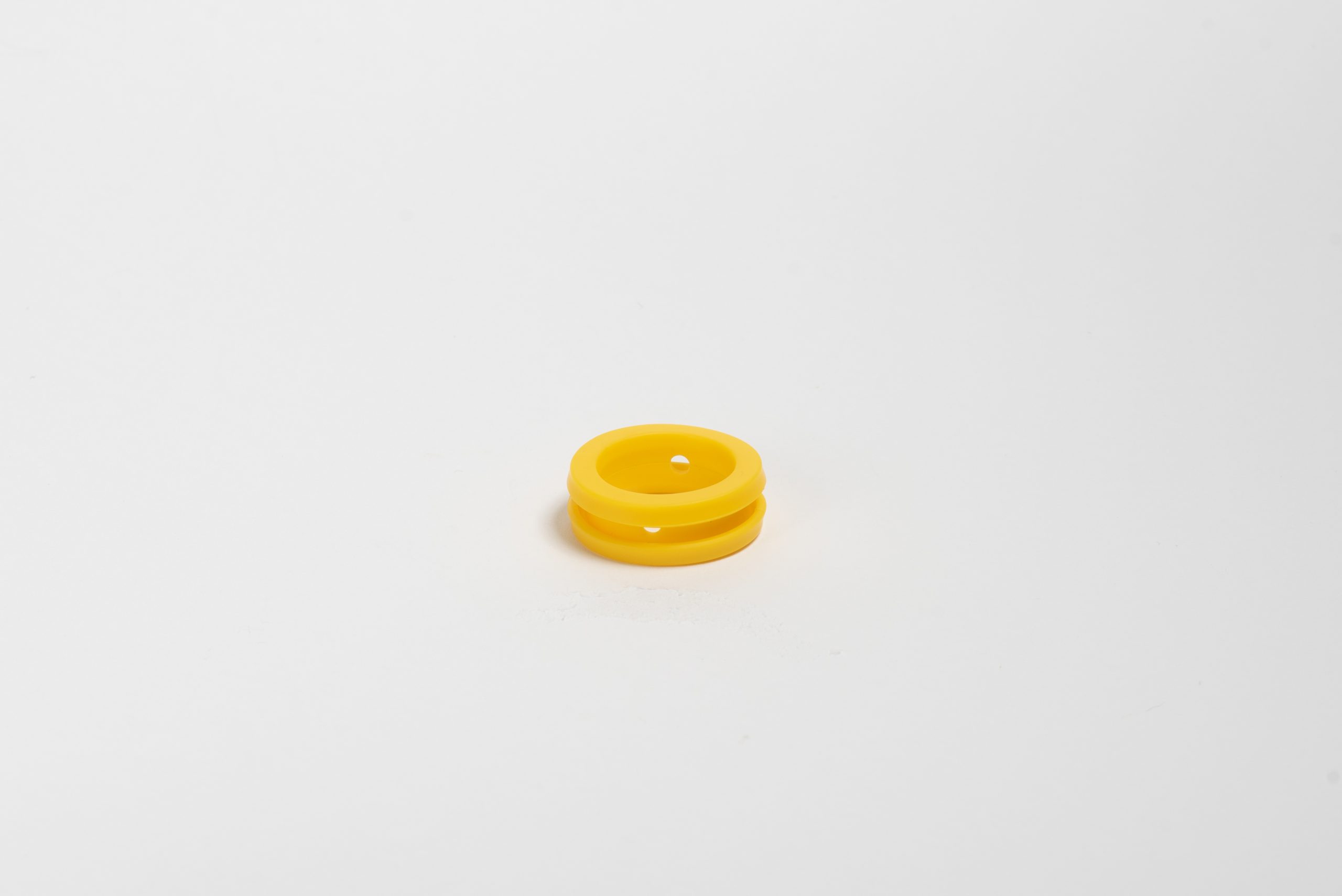
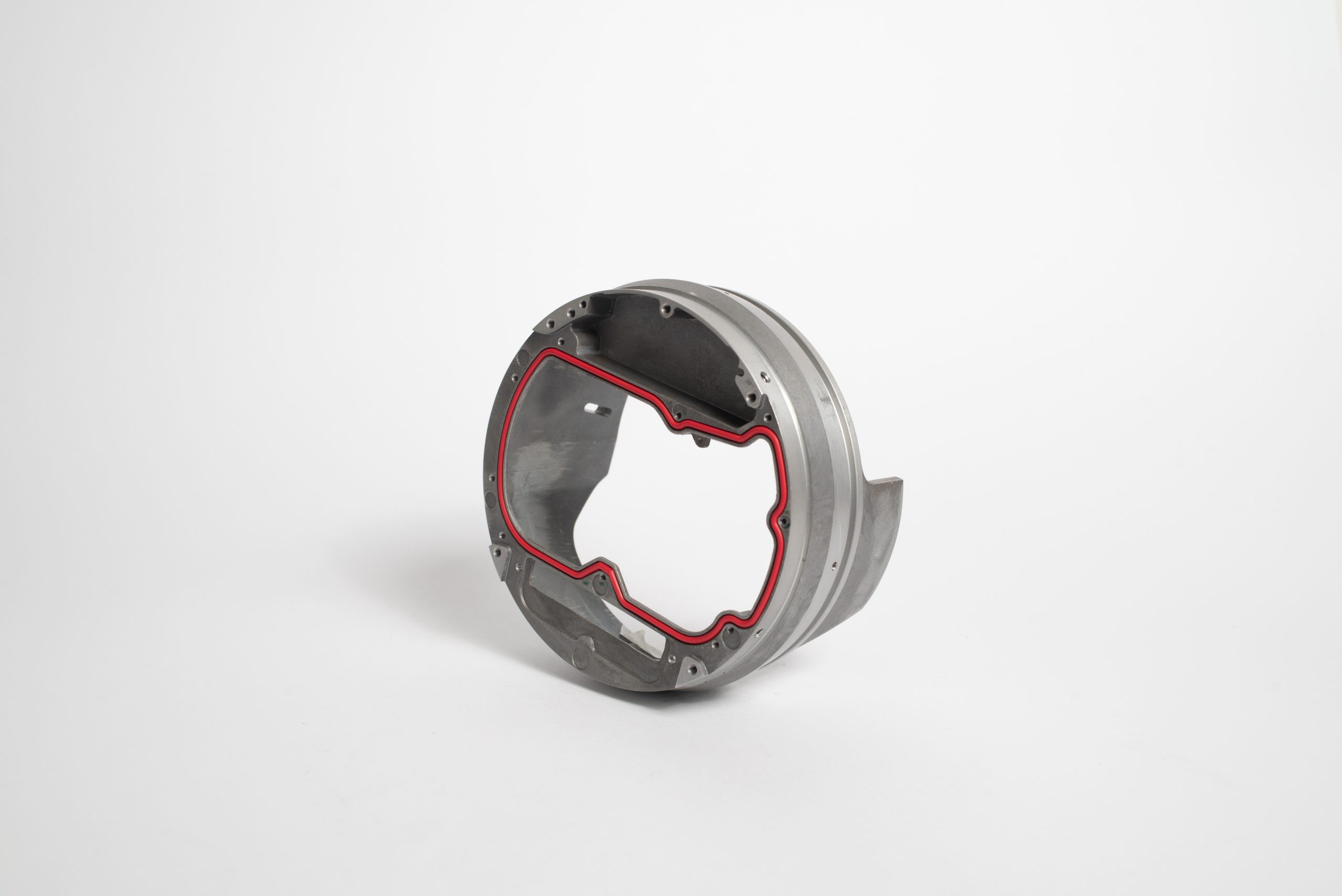
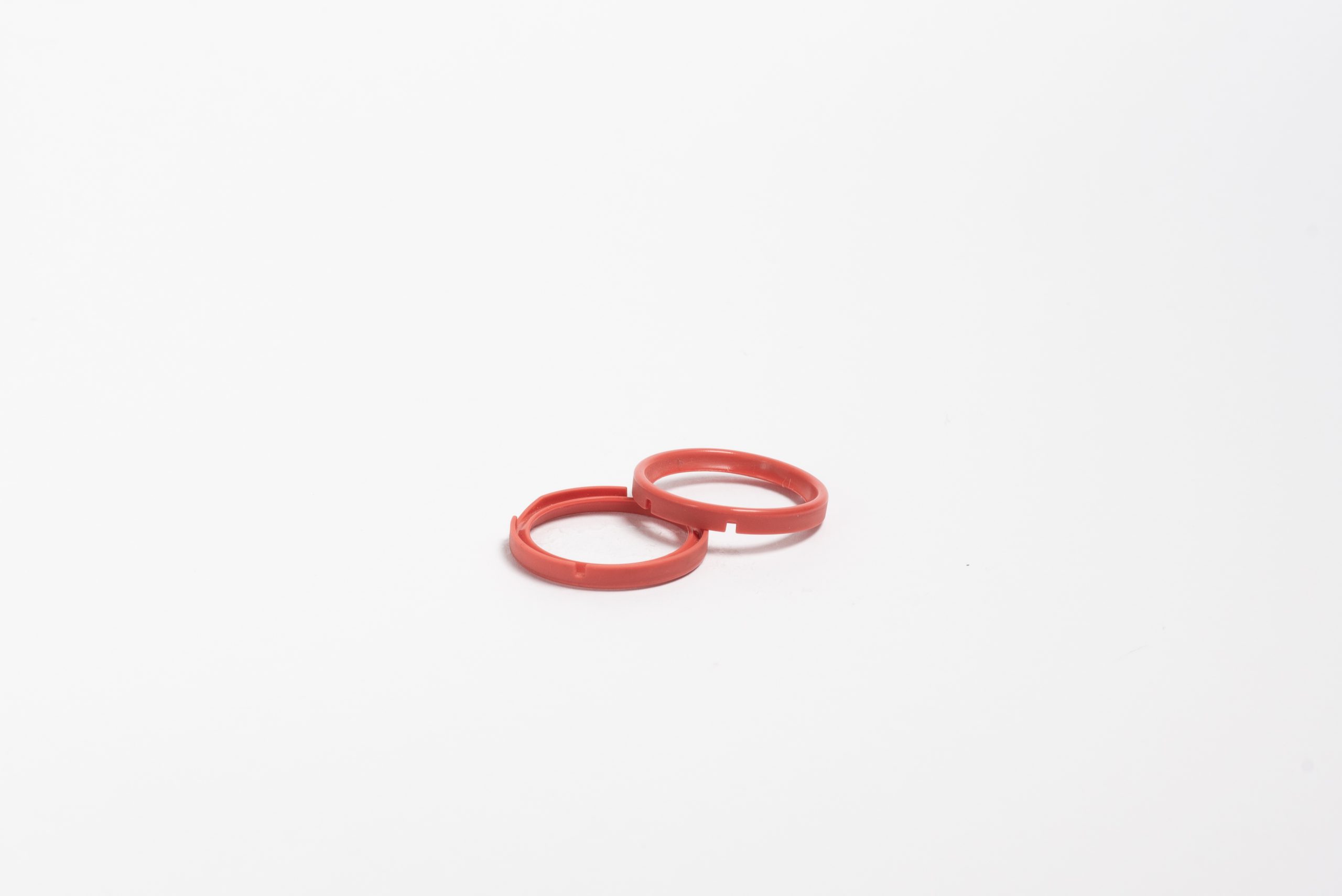
Energy Absorbing Solutions:
Energy absorbers, dampers and cushions are dynamic applications of rubber obtained due to
elastomer’s unique characteristics. Rubber is characterized by high elasticity and high viscosity; it has
great linear flexibility and can be stretched to break without losing its elasticity and can withstand
alternating stress without fatigue. Rubber is incompressible and resilient and demonstrates torsional
strength and excellent damping characteristics. When exposed to constant vibrations or to sudden
shocks, special rubber compounds outperform other materials by reducing shocks and vibrations.
Rubber is easily vulcanized to metal chassis and can be molded at almost every shape and form,
which makes it the ultimate solution for every dynamic application. At SKM we offer design support
and professional manufacturing of over-molded energy absorbers, damper and cushions for various
applications including stabilizers for small industrial PCB cards bonded shock and energy
absorbers for ground military applications, bonded absorbers for aviation, and bonded
dampers for various industrial applications, ensuring long lasting stabilized solutions to perfectly
meet your applications.
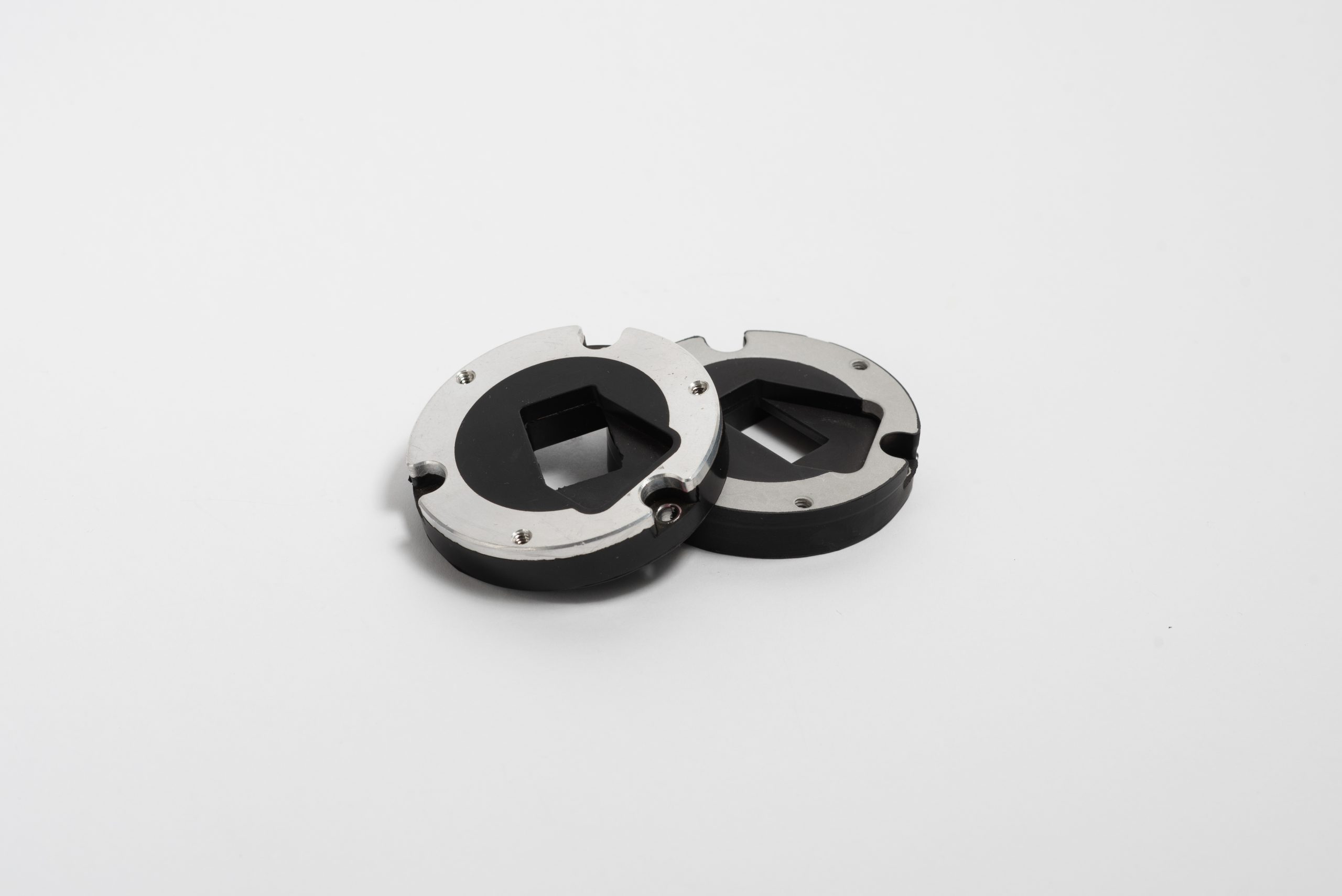

Electrical Conductivity - EMI / RFI / ESD Solutions:
Electrical conductivity is a less known feature of rubber compounds. Today innovative technologies
allow enrichment of special compounds with conductive additives such as silver-plated aluminum,
copper and glass, nickel-plated aluminum and graphite, conductive carbons, silver and more while
keeping a significant portion of rubber’s basic properties thus allowing variety of uses for every
industry. Compounds and seals for electrical applications are divided into several categories based
on their electrical surface or volume resistivities and their decay rates. These features are defined by
the compound’s composition and resistance.
Conductive rubber characterized by surface resistivity in the range of 1×10 2 – 1×10 5 ohms/ square cm. and have decay rates measured in nanoseconds. ESD rubber are considered to be static dissipative and have a surface resistivity in the range of 1×10 6 – 1×10 9 Ohms/square cm. and allow for dissipation of electrical charges within milliseconds. Anti-Static rubber show surface resistivity in the range of 1×10 10 – 1×10 11 Ohms/square cm. and are those that inhibit triboelectric charging. Turboelectric charging is the build-up of an electric charge by rubbing one material with another material. These materials provide a very slow rate of decay of static charges from a hundredth of to several seconds. Insulative rubber have surface resistivity greater than 1×10 12 Ohms/square cm. and they do not contain any conductive additives in their formulations.
Conductive rubber characterized by surface resistivity in the range of 1×10 2 – 1×10 5 ohms/ square cm. and have decay rates measured in nanoseconds. ESD rubber are considered to be static dissipative and have a surface resistivity in the range of 1×10 6 – 1×10 9 Ohms/square cm. and allow for dissipation of electrical charges within milliseconds. Anti-Static rubber show surface resistivity in the range of 1×10 10 – 1×10 11 Ohms/square cm. and are those that inhibit triboelectric charging. Turboelectric charging is the build-up of an electric charge by rubbing one material with another material. These materials provide a very slow rate of decay of static charges from a hundredth of to several seconds. Insulative rubber have surface resistivity greater than 1×10 12 Ohms/square cm. and they do not contain any conductive additives in their formulations.
Read More
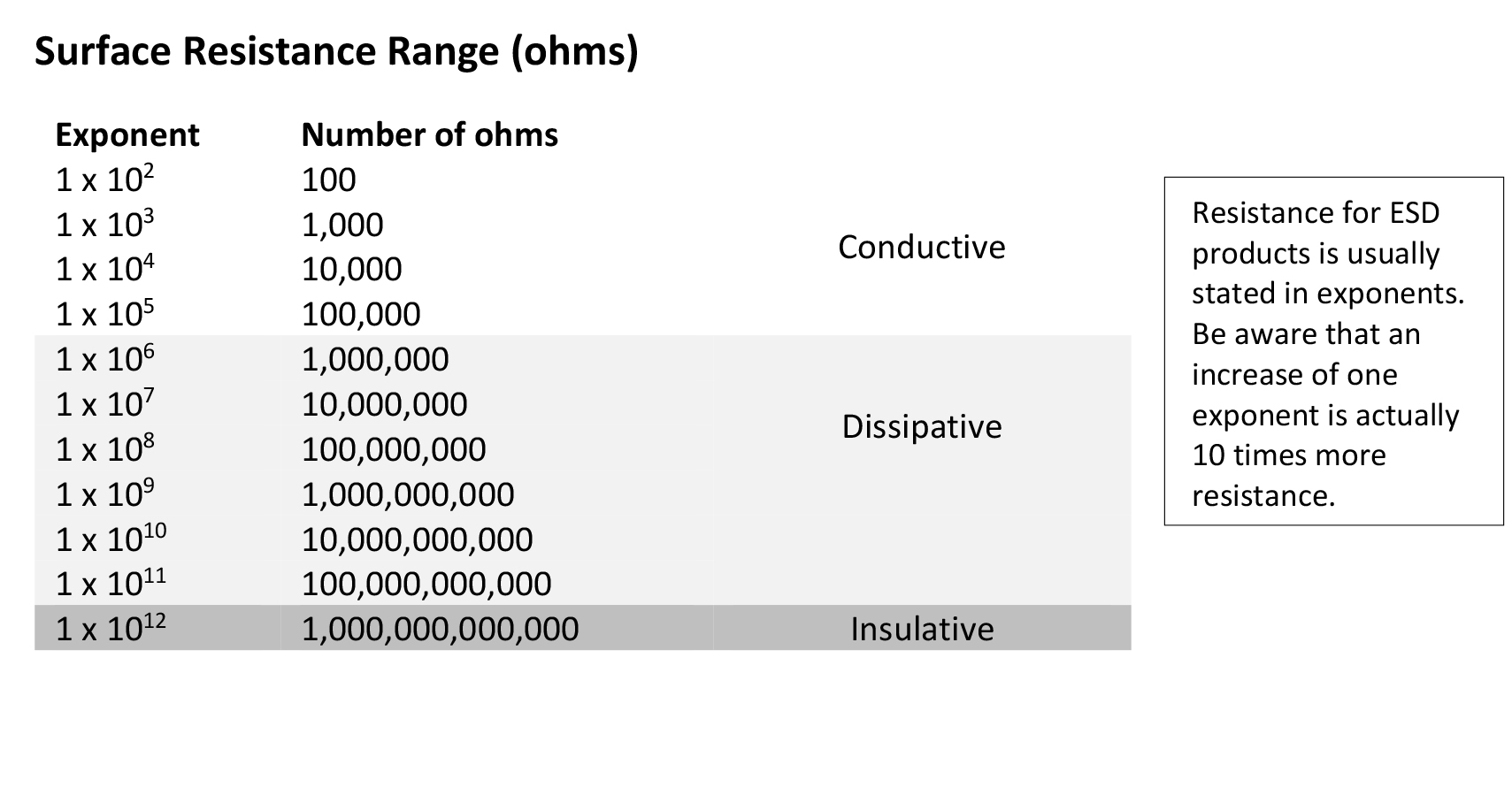
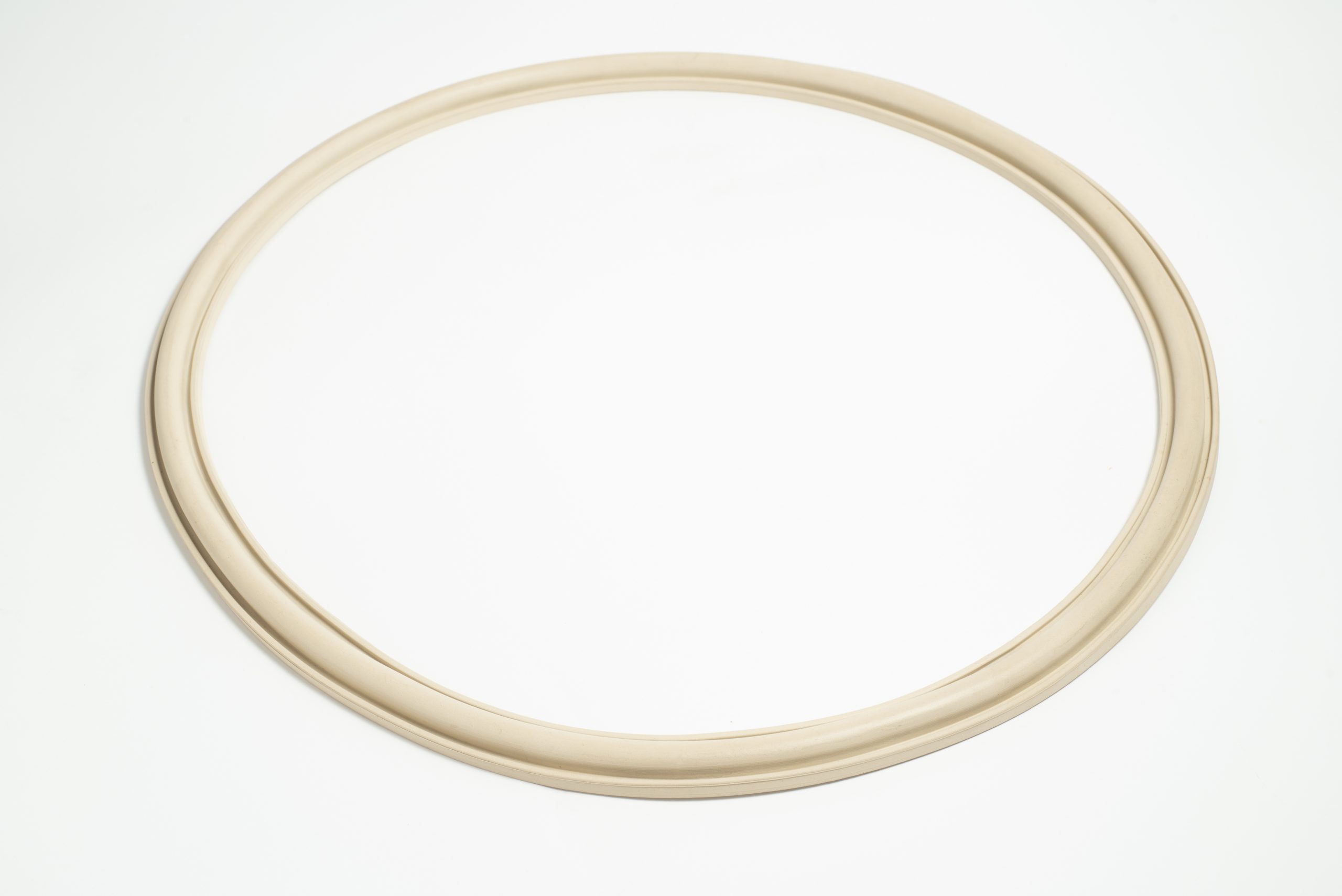
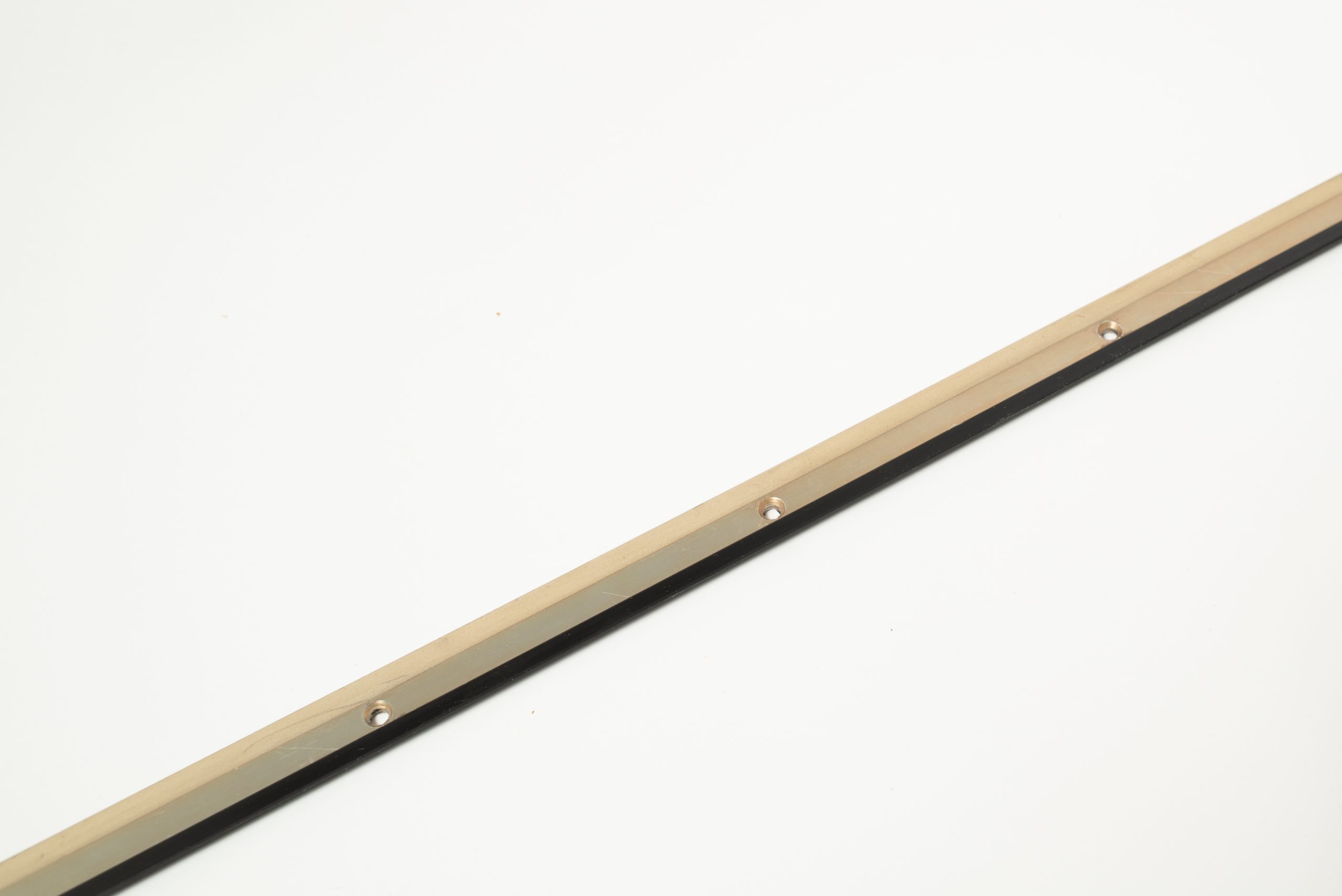
Friction Solutions:
Today various industrial applications are based on precision and technical rubber are also known to
be sensitive to friction, whether low-friction in dynamic applications, or high-friction in static and
safety applications.
The Coefficient of Friction is a property appointed to the material, and in rubber it derives mainly
from the actual structure of the compound; however, it can be partly changed (both increased and
decreased) a unique and precise mold treatment.
SKM participates as an active partner at HORIZON2020 program at several research and development projects, focusing on friction and surface activation of rubber and seals. Today as a part of a consortium and based on “MoludTex” Technology, SKM offers reliable and workable solutions for optimization of friction according to applications, service conditions and client’s specifications. Our group provides a comprehensive tailor-made solution, we implement advanced tribology simulations and mathematical prediction models, innovative 3Dmicro laser-engraving process, design and manufacturing of ultra-precision molding tools, precision verification and measurement abilities and molding of high-performance rubber parts.
Our MouldTex Technology allow us to decrease or increase friction of a given rubber part, by implementing a patent registered surface activation process. Innovative software packed combine with 3D-micro laser engraving and plasma treatments allow us to design and produce tool cavities that emboss unique surface finish on the molded rubber parts directly off-molding. Our MouldTex technology perfectly fits with all molding technologies including compression molding, transfer compression and injection molding.
The outcomes of MouldTex technology are highly demanded by the medical and the military and aviation markets for its outstanding functional advantages such as friction reduction, friction increase, as a preliminary and accurate process for pre-bonding rubber to exotic material, and by the automotive market for its acoustic noise reduction and its esthetic and super elegant look-and-feel. MouldTex technology is accurate, safe, and environmentally friendly and it completely eliminates the need to surface finish each individual part after molding.
MouldTex technology does not require changes to rubber compounds and does not increase the unit cost. The one-time investment is associated with the required simulations and the design for production of MouldTex unique laser-engraved tooling.
SKM participates as an active partner at HORIZON2020 program at several research and development projects, focusing on friction and surface activation of rubber and seals. Today as a part of a consortium and based on “MoludTex” Technology, SKM offers reliable and workable solutions for optimization of friction according to applications, service conditions and client’s specifications. Our group provides a comprehensive tailor-made solution, we implement advanced tribology simulations and mathematical prediction models, innovative 3Dmicro laser-engraving process, design and manufacturing of ultra-precision molding tools, precision verification and measurement abilities and molding of high-performance rubber parts.
Our MouldTex Technology allow us to decrease or increase friction of a given rubber part, by implementing a patent registered surface activation process. Innovative software packed combine with 3D-micro laser engraving and plasma treatments allow us to design and produce tool cavities that emboss unique surface finish on the molded rubber parts directly off-molding. Our MouldTex technology perfectly fits with all molding technologies including compression molding, transfer compression and injection molding.
The outcomes of MouldTex technology are highly demanded by the medical and the military and aviation markets for its outstanding functional advantages such as friction reduction, friction increase, as a preliminary and accurate process for pre-bonding rubber to exotic material, and by the automotive market for its acoustic noise reduction and its esthetic and super elegant look-and-feel. MouldTex technology is accurate, safe, and environmentally friendly and it completely eliminates the need to surface finish each individual part after molding.
MouldTex technology does not require changes to rubber compounds and does not increase the unit cost. The one-time investment is associated with the required simulations and the design for production of MouldTex unique laser-engraved tooling.
Read More
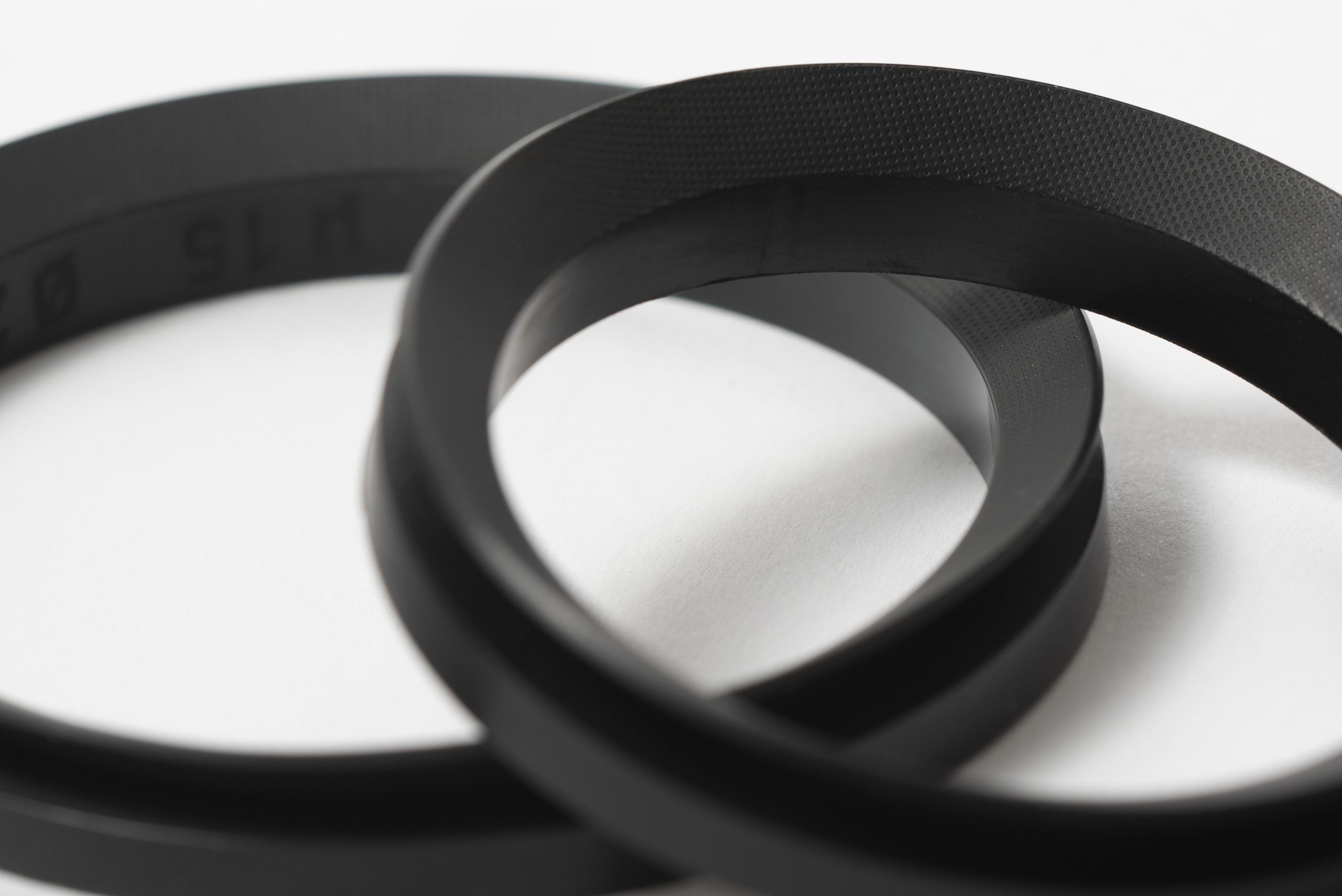
Friction reduction surfac
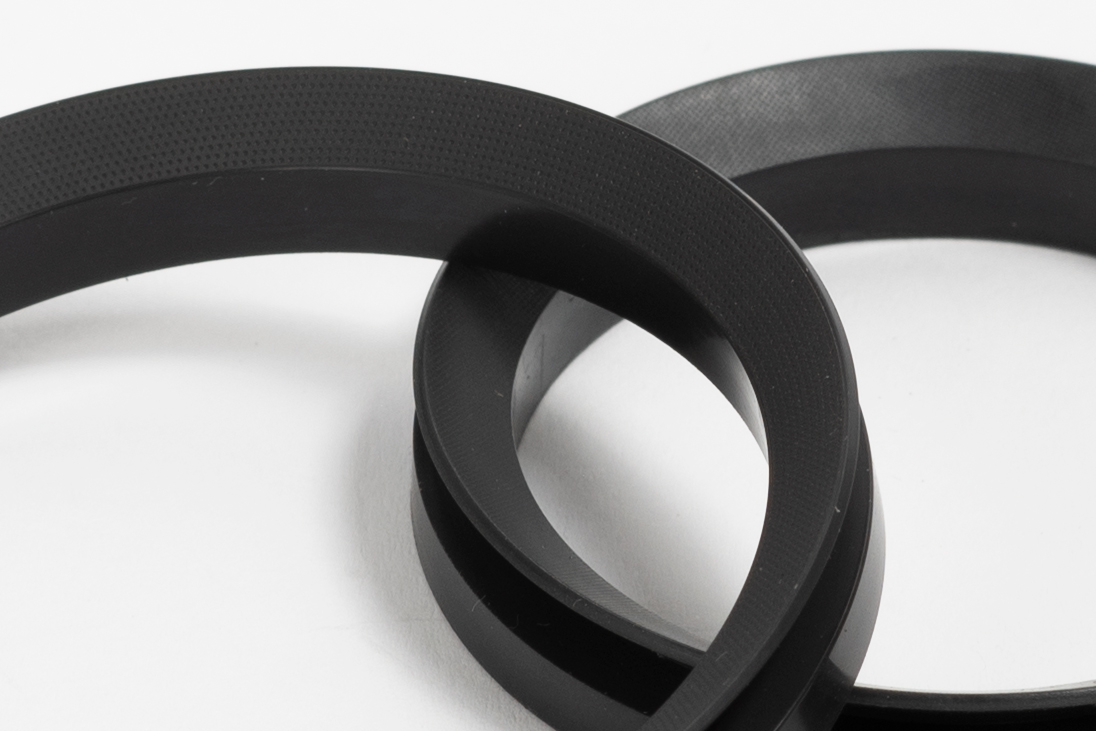
Friction reduction surfac
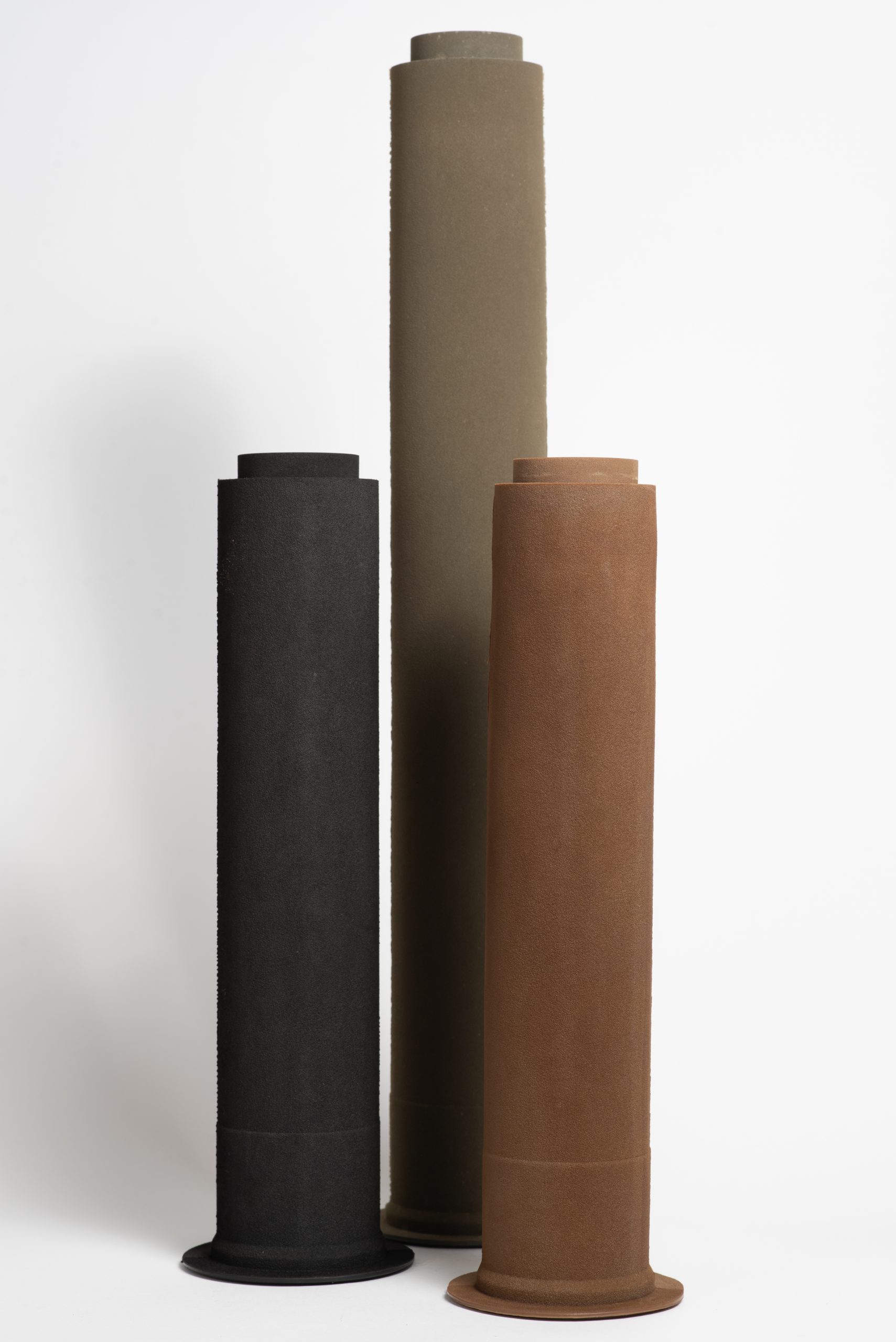